3D Printing and 3D Printers
My experience with 3D printing and 3D printers extends over five years.
- Building and Modifying: I've built, modified, and upgraded 3D printers.
- Prototyping: I've introduced 3D printing as a tool for prototyping in the last two companies I worked for and helped suggest which 3D printers to purchase.
- Slicer Software: I've used many slicer software and am familiar with all the settings required to produce a high-quality Gcode.
- Troubleshooting: I'm highly capable of solving any issues that come up during 3D printing, whether it's hardware or software-based. This capability was gained through years of encountering challenges.
- CAD Modeling: I've created and designed CAD models that are 3D printer-friendly and added removable supports when needed to facilitate the printing.
- Printer Monitoring: I use a Raspberry Pi to communicate with and monitor the 3D printers using OctoPrint.
- Portfolio: Visit my photo gallery to see 3D printed designs and parts I've worked on.
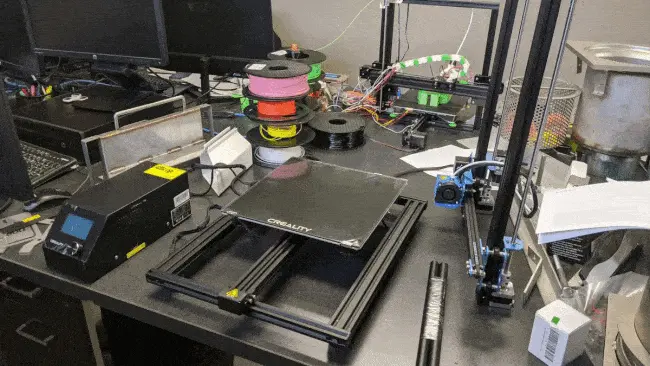
Indexer Designs
I was a part of a team tasked with redesigning the gam indexer across the entire plant, as the existing ones were identified as a major source of foreign material.
- Concept Development: I came up with two different principles and used AutoCAD Inventor to create multiple concepts for each principle.
- Animation: I used Inventor Studio to animate the indexer to illustrate the movement of the gams.
- Presentation: The generated concepts were presented to management, and one concept was chosen for creating a test rig.
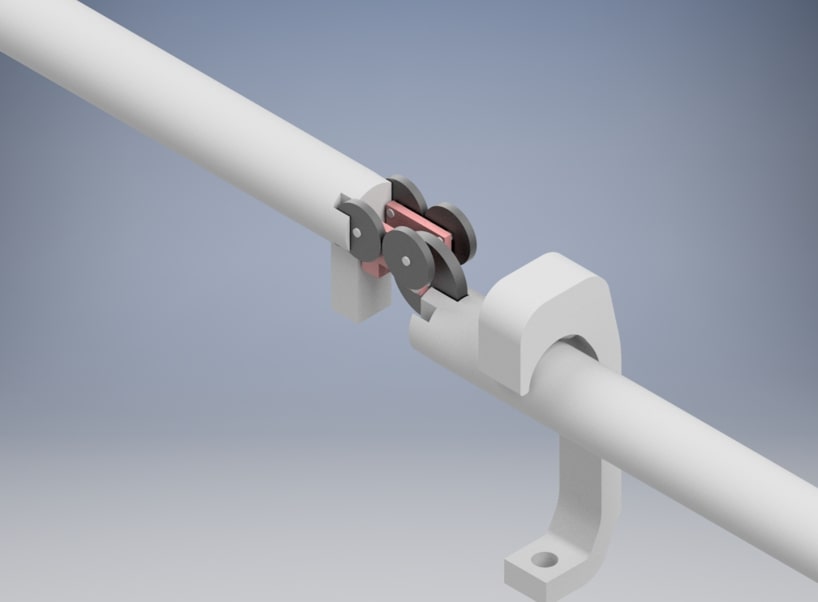
Lock and Key Mechanism Re-design and Improve
The Food Industry often deals with a problem where employees dump the waste caught in basket strainers into drain outlets, leading to blockages in their plumbing systems. A simple solution was needed to discourage this behavior.
- Global Drain Technologies offers an optional secondary strainer that prevents any waste from going down the drain.
- The optional strainer needed to be corrosion resistant, easy to remove, sanitary, and waterproof with no possible harbouring points.
- The solution for easy removal was implemented in the form of a lock that can be released using a magnetic key.
- Researched, discussed with university professors and tested multiple metals that met the following requirements:
- High corrosion resistance
- Possessed magnetic properties
- Could be machined without special equipment
- Were easily obtainable and reasonably priced
- Tested Austenitic, Martensitic, and Ferritic types of Stainless steel in salt water to confirm their corrosion resistance capabilities.
- Conducted numerous tests with variations of the components with the help of prototyping with a 3D printer.
- Found a combination of a magnet and a metal that worked together.
- Researched O-ring standards and test fitted different sizes to find an appropriate option for the pin and hole sizes. I later dimensioned the correct grove size based on the standard to get correct sealing.
- Contacted CNC machining service providers for quotes once a working prototype was achieved.
- Designed a key for the lock that was easy to manufacture, simple, food safe, and aesthetically pleasing. Outsourced the magnet required for the key from an online vendor and confirmed its capabilities before committing to a large order.
Slot Drain Tab-less Design
Typically, all slot drains have welded tabs in their slots to maintain the slot width and shape during transportation and installation. However, these tabs can create sanitary problems as they form harbouring points and pose challenges during cleaning.
- To eliminate the need for the tabs, I designed rib-like structures to replace them and tested them using Inventor stress analysis.
- Various configurations of the ribs were tested using Inventor's stress analysis with the help of the parametric table tool.
- The parametric table allows for testing multiple constraints simultaneously to optimize for a specific target.
- The target was to only allow for a specific amount of displacement at the neck of the slot drain, with the least amount of material required.
- I set upper and lower limits to the constraints, then used the stress analysis study to check every possible combination of the constraints values to find and optimize for the best solution.
- To decrease the material required to manufacture the ribs, I used the frame generator feature of Inventor. This feature removes material from the ribs that do not contribute to the function of the model as they experience little to no stress.
- The best rib design was then used in another simulation to find the needed amount of ribs to install on a single slot drain run.
- I created drawings and DXF files for the sheet metal components to get it ready for production. The ribs were then produced and welded on a slot drain for real life testing.
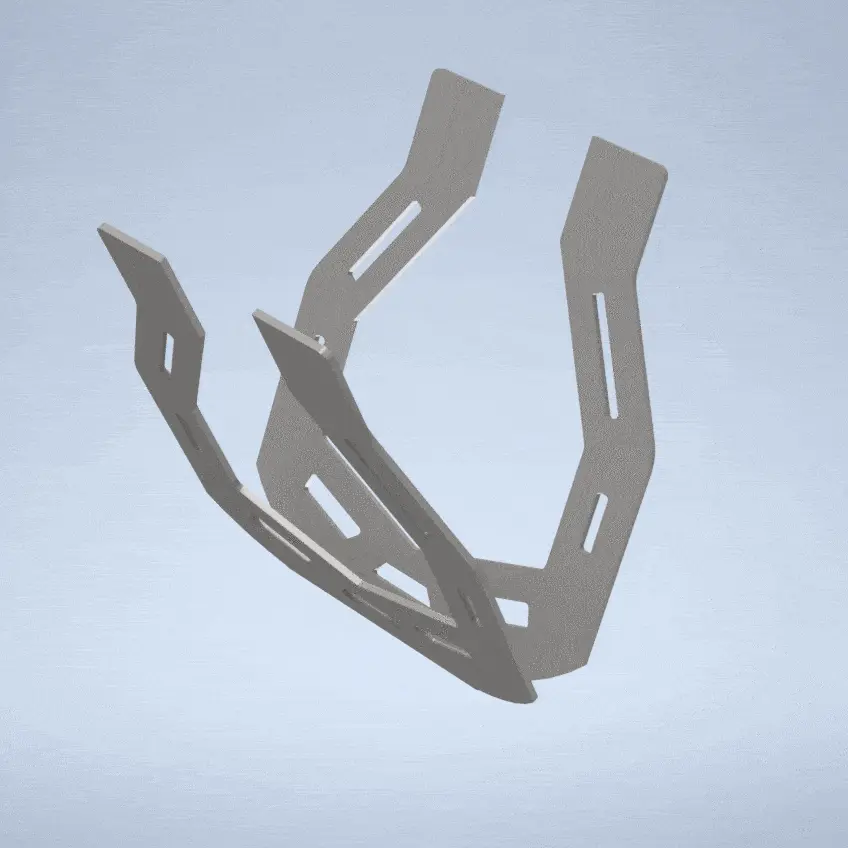
Production / Welding Jigs and Fixtures
During my work at GDT, I created multiple jigs and fixtures to aid in production and welding. The main objective of the jigs and fixtures are to put constraints on the components during the welding process. The jigs must be simple, easy to use, reliable, and capable of reproducing consistent results.
- The jigs served to increase the speed of production, and improve the consistency between products and batches.
- Designing the jigs involved the help and feedback of the production team as they are the ones who will use them.
- I received requests and built specific tools or jigs that the welders thought could improve the production process.
- I spent many hours on the production floor with the production team to understand their actual needs.
- The jigs were mainly made from laser cut sheet metal welded together, and others were 3D printed.
Basin Lid Lifting Tools
During my work, I was tasked with figuring out a standard design for a lift tool and feature to eliminate the need for using direct contact with the drain. The feature and tool must be simple, sanitary, and easy to clean.
- All the basins require skin contact to lift up, which is considered unsanitary, and is ergonomically taxing.
- Involved the sales team in the prototyping process to get feedback on what the customer needs.
- Prototyping went through multiple iterations after getting the feedback until a design was decided on.
- Lids with the lifting tools was first introduced into a specific series, and then later will be introduced to the rest of the slot drains.
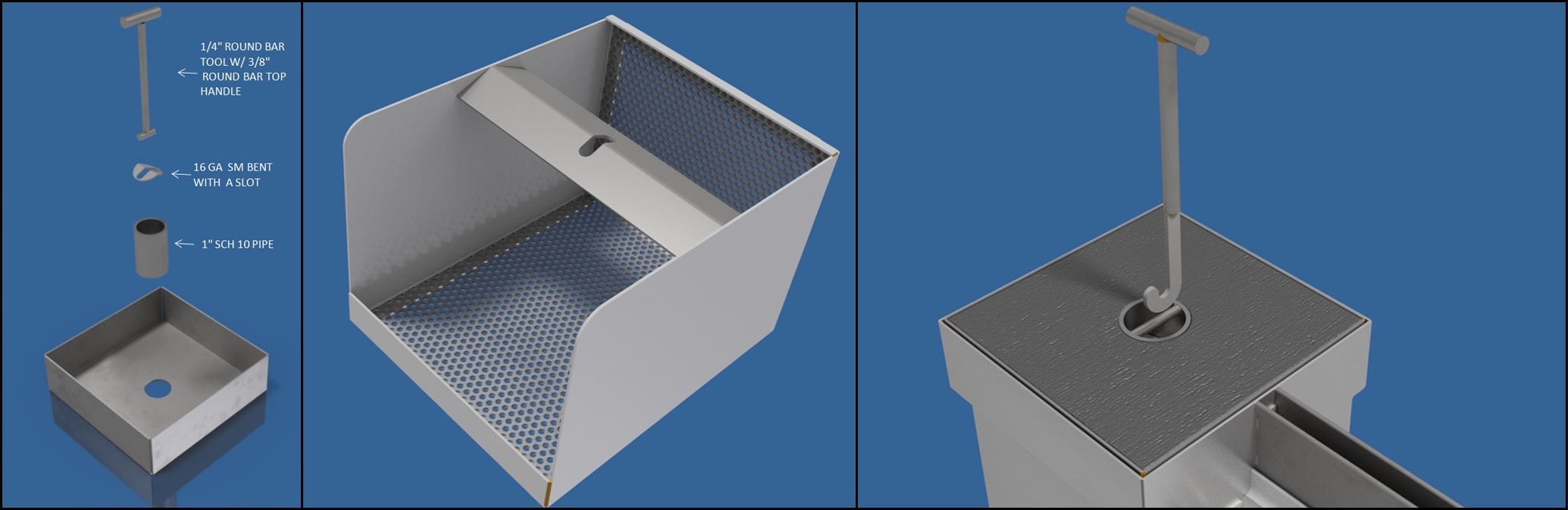
Demo Unit Models
I designed models that helped the sales team demonstrate the features of the drain products. The models were based on the current products but modified to highlight specific aspects of the drains. I also designed and 3D printed smaller models of the slot drain products for the sales team to use as promotions and sales aids.
- Communicated with the sales team during the design process to create the desired units.
- Worked closely with the production team to manufacture the units according to the requirements.
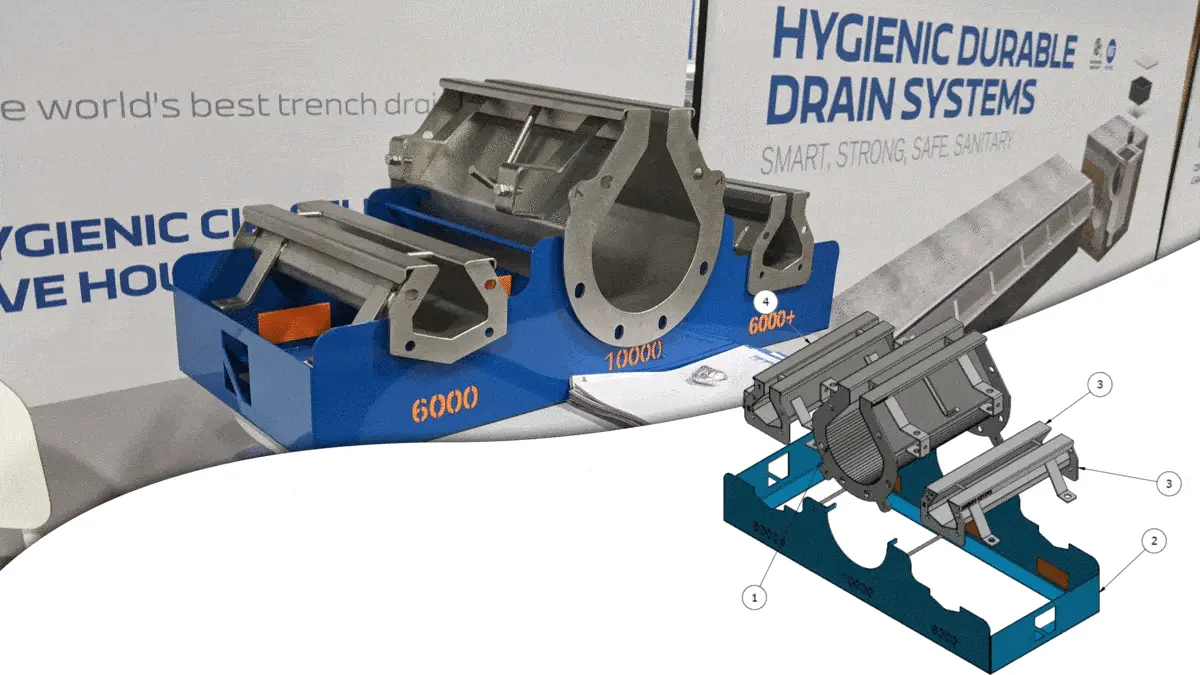
Macdon Electrical Generation Project
- A team project to design a stand alone system that would be integrated onto a combine header for Macdon that required little to no modifications to the header
- Took the project through the engineering design process, from define phase through problem statement and objectives
- Defined target specifications through customer needs and created a project metrics list, constraints and limitations, then a project schedule with a Gantt Chart
- Generated concepts through brain storming sessions then used advantages/disadvantages list and weighing matrix for the criteria then using the criteria to score the concepts
- Chose the concept, performed calculations and dimensioning of the components, then created a BOM for the system
Machine Design Projects
- The class included three design projects the involved producing a solution for a problem with a specific set of parameters and limits
- The first project required the design of a structure that would be able to support a force and achieve a minimal structure weight
- The second project required the design of a shaft that needs to transmit torsional power and that won't fail due to yielding, fatigue, or fracture before a specific amount of cycles
- The third project involved the development of a transmission system for a windmill. Three possible power transmission systems were considered: a belt drive, chain drive, and gear drive. The gear drive was selected and a complete transmission system was developed along with the shaft, keys, seals, retainer rings, ball bearings, and lubrication requirements, etc.
- During the projects, Apmonitor and Matlab were used to solve and iterate for the best combination of parameters to achieve the least weight
- Used SolidWorks to render the designed systems and perform FEA analysis and calculate factors of safety
- Produced detailed and comprehensive reports for each project. Link
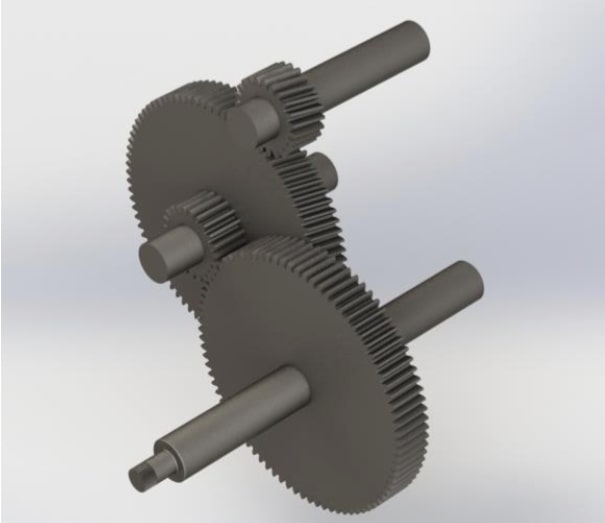
Advanced Graphical Communications (GD&T)
- Successfully finished a class about Geometric Dimensioning and Tolerancing (GD&T)
- Learned and practiced the standards in accordance with the ASME Y14.5-2009 Dimensioning and Tolerancing
- Covered the hierarchy, application and tolerance zones for location, orientation, size and form controls
- Completed assignments that involved real mechanical systems / assemblies to include differing manufacturing technologies, materials, and functionalities
- Used advanced graphical communications methods to effectively communicate design intent
Name Plate Designs
- Created completely custom name tags for friends and family members
- Used Autodesk Inventor to create the name tags, with the help of Autodesk Meshmixer for modifying the mesh for the STL files
- Meshmixer was also used to generate and separate complexes to prepare the models for dual extrusion 3D printing
- Used OpenSCAD to generate a planetary gear assembly that can be fully 3D printed all at once
- Prototyped multiple models to get the correct tolerance between the gears and account for the capability of the 3D printer to achieve a model that can rotate with little effort
- Used anatomically correct teeth models to create a dental articulator assembly. Then modified the mesh, sliced, and dual extrusion 3D printed it
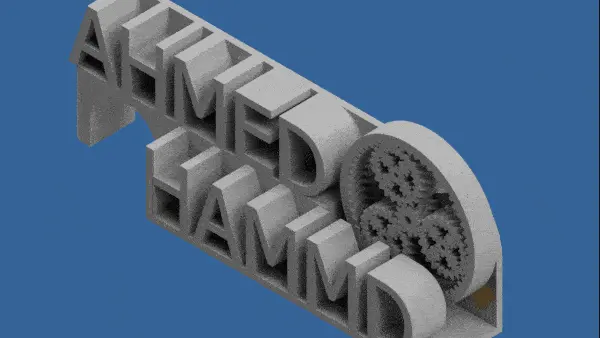