Round Area Drain Design And Production
As a part of my responsibilities at GDT, I was entrusted with the task of researching, designing, and introducing a new product to the company's catalog. This involved conducting extensive research on the customer's needs and the current competitive solutions available in the market. In addition to that, I also reviewed and summarized the National Sanitation Foundation (NSF) specifications to ensure that the designs adhered to their strict guidelines for food safety standards.
I involved all the stakeholders in the process including management, production, engineers, and company owners. With their input, I was able to create a list of customer needs and design different solution prototypes, which were then 3D printed. The area drain product included multiple sub-products that completed the assembly, some standard, others optional. In the process, we faced manufacturing limitations and other challenges, all of which were resolved with adjustments and redesigning.
Ultimately, the manufactured prototypes were used to close a large deal with a major Canadian food producer after implementing solutions to their proposed unique problems. I also implemented a solution to prevent the cover from rotating to avoid slipping. For a detailed account of the project progress, please refer to the attached record: [Link]
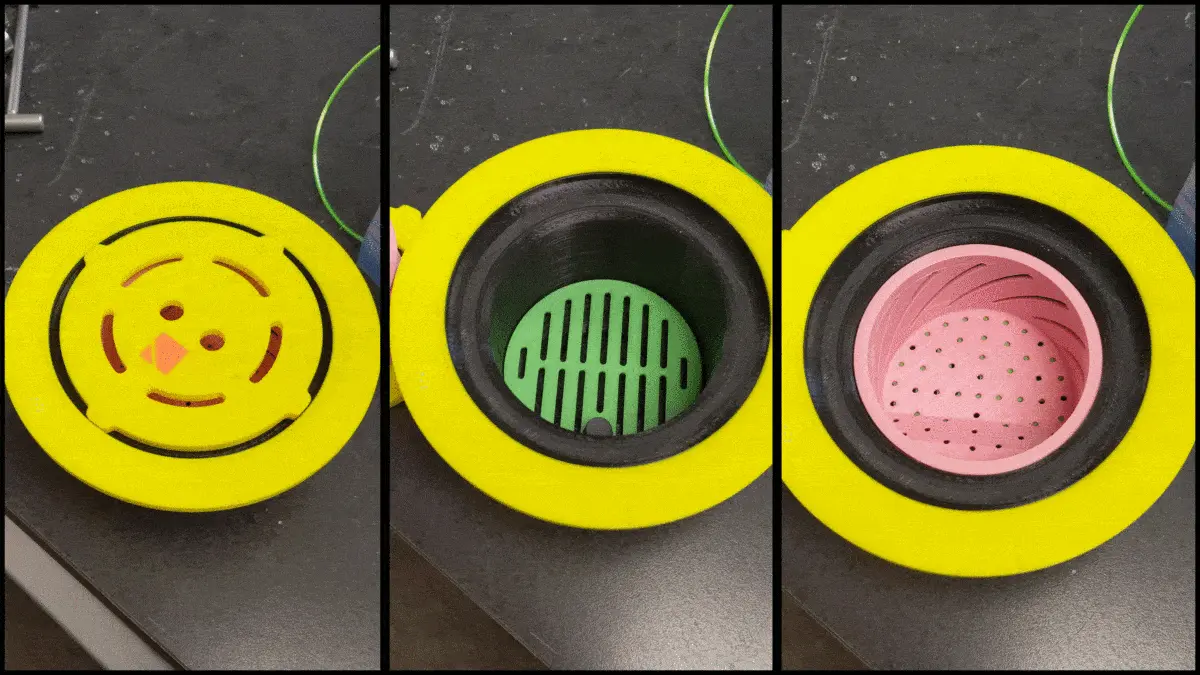
Lock and Key Mechanism Re-design and Improve
The Food Industry often deals with a problem where employees dump the waste caught in basket strainers into drain outlets, leading to blockages in their plumbing systems. A simple solution was needed to discourage this behavior.
- Global Drain Technologies offers an optional secondary strainer that prevents any waste from going down the drain.
- The optional strainer needed to be corrosion resistant, easy to remove, sanitary, and waterproof with no possible harbouring points.
- The solution for easy removal was implemented in the form of a lock that can be released using a magnetic key.
- Researched, discussed with university professors and tested multiple metals that met the following requirements:
- High corrosion resistance
- Possessed magnetic properties
- Could be machined without special equipment
- Were easily obtainable and reasonably priced
- Tested Austenitic, Martensitic, and Ferritic types of Stainless steel in salt water to confirm their corrosion resistance capabilities.
- Conducted numerous tests with variations of the components with the help of prototyping with a 3D printer.
- Found a combination of a magnet and a metal that worked together.
- Researched O-ring standards and test fitted different sizes to find an appropriate option for the pin and hole sizes. I later dimensioned the correct grove size based on the standard to get correct sealing.
- Contacted CNC machining service providers for quotes once a working prototype was achieved.
- Designed a key for the lock that was easy to manufacture, simple, food safe, and aesthetically pleasing. Outsourced the magnet required for the key from an online vendor and confirmed its capabilities before committing to a large order.
Drain Load Testing
I played a key role in conducting multiple tests with various drain products to ensure they meet the load specifications for industrial applications.
- Understanding the Standards: I learned and understood the DIN EN 1433 classification, which is the standard for drainage channels for vehicular and pedestrian areas.
- Product Classification: The drain products were designed to achieve class E or F, suitable for high wheel loads such as ports, docks, and aircraft hangars.
- Preliminary Testing: I used Inventor stress analysis to digitally load test the products as a preliminary check to verify the likelihood of physical testing success.
- Testing Procedure: After understanding the requirements, the testing was outsourced to the University of Manitoba Industrial Technology Center. I wrote a proposal outlining all the test requirements and a detailed step-by-step procedure.
- Review and Modification: I studied the test results, and if the specimens didn't reach the desired class, modifications were made to improve the weakest parts.
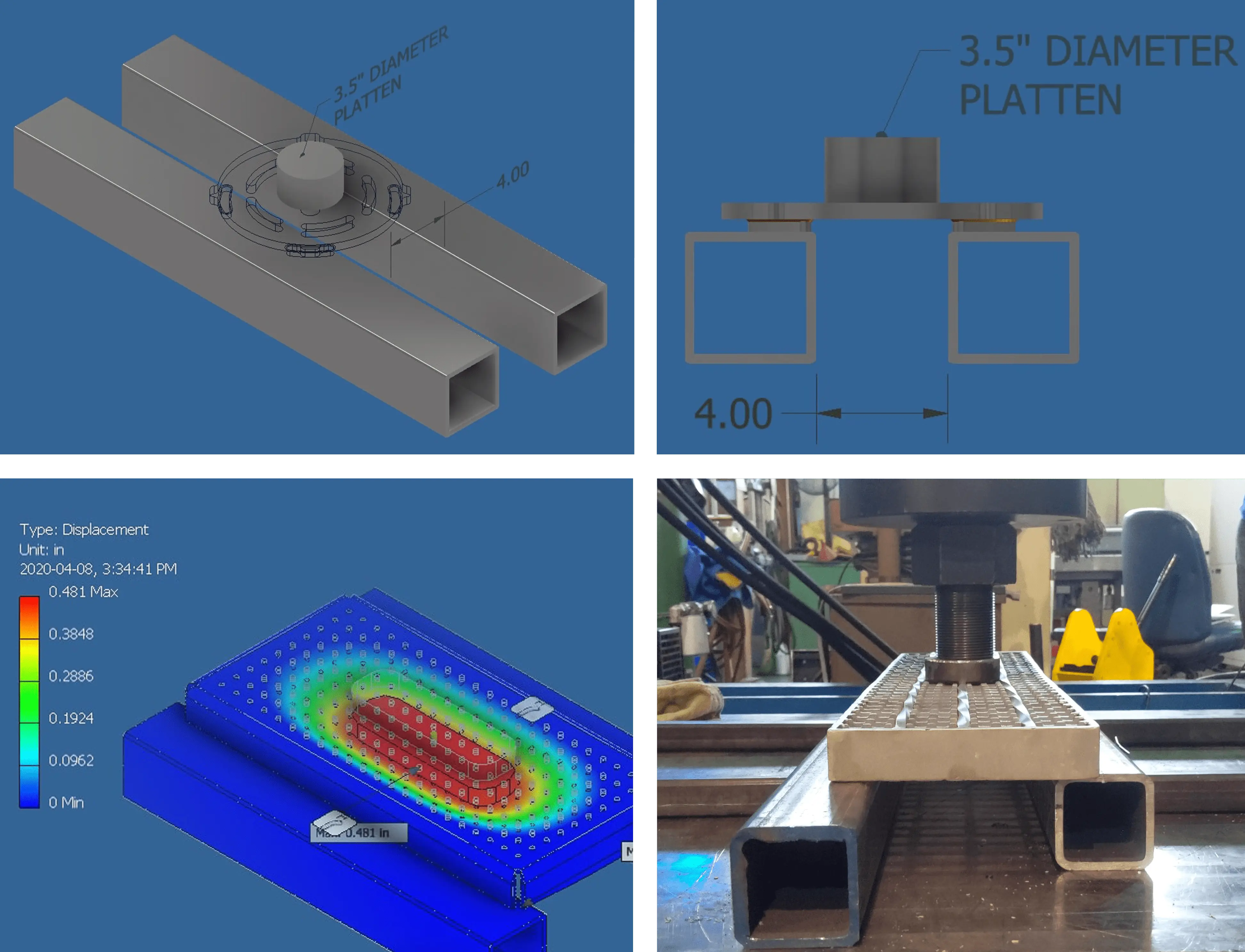
Blender Renders
I self taught the open-source 3D computer graphics software Blender. I used Blender to render models for the sales team, and for creating catalogs for the company's products. I created a step by step procedure manual for installing Slot and Trench drain products, and rendered models to highlight specific unique and innovative features that make slot drains stand out against the competition.
Slot Drain Tab-less Design
Typically, all slot drains have welded tabs in their slots to maintain the slot width and shape during transportation and installation. However, these tabs can create sanitary problems as they form harbouring points and pose challenges during cleaning.
- To eliminate the need for the tabs, I designed rib-like structures to replace them and tested them using Inventor stress analysis.
- Various configurations of the ribs were tested using Inventor's stress analysis with the help of the parametric table tool.
- The parametric table allows for testing multiple constraints simultaneously to optimize for a specific target.
- The target was to only allow for a specific amount of displacement at the neck of the slot drain, with the least amount of material required.
- I set upper and lower limits to the constraints, then used the stress analysis study to check every possible combination of the constraints values to find and optimize for the best solution.
- To decrease the material required to manufacture the ribs, I used the frame generator feature of Inventor. This feature removes material from the ribs that do not contribute to the function of the model as they experience little to no stress.
- The best rib design was then used in another simulation to find the needed amount of ribs to install on a single slot drain run.
- I created drawings and DXF files for the sheet metal components to get it ready for production. The ribs were then produced and welded on a slot drain for real life testing.
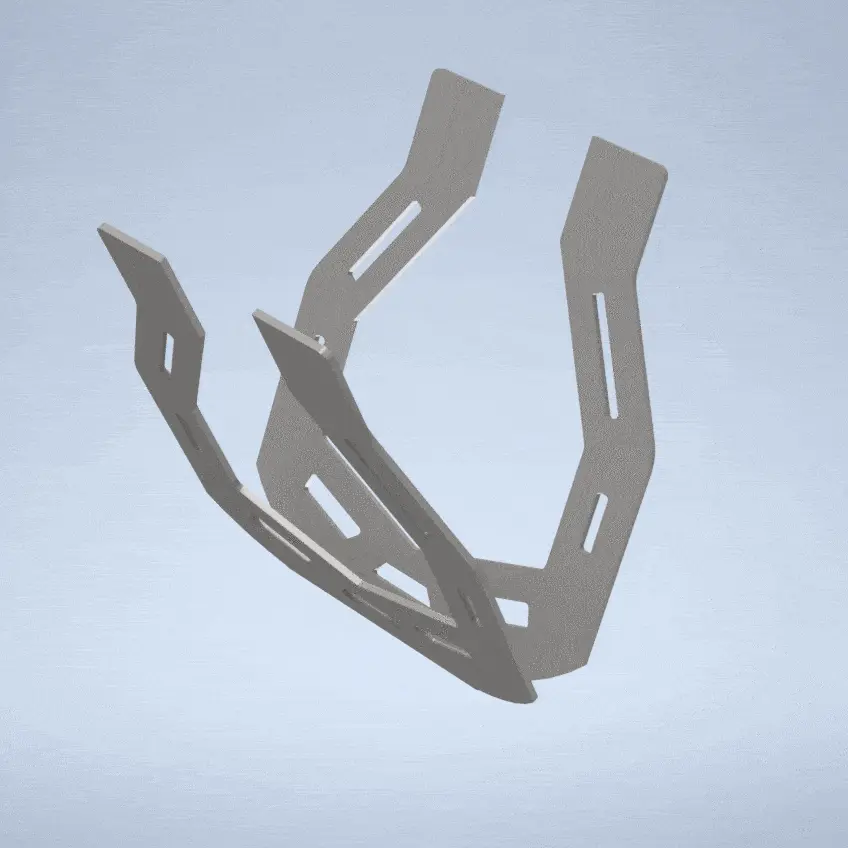
Plastic Drain Improvements
Tasked with the responsibility of improving the production readiness of the plastic slot drain, I undertook several steps to build and assemble the drain runs. This involved creating an assembly line list of materials and equipment required, work in progress, and assembly steps. I also designed multiple jigs to aid each step of the assembly, and a table for the mitre saw that featured a fixturing system and a back fence.
Working closely with the production team, I ensured that the assembly process was conducted efficiently and correctly. This also extended to designing standard and custom basins to meet customer needs, creating stainless steel elbows from one-piece sheet metal to reduce alignment time during welding, and working with a local plastic extrusion company to address assembly challenges. Furthermore, I visited client sites to oversee the drain installation process and gather direct customer feedback.

Production / Welding Jigs and Fixtures
During my work at GDT, I created multiple jigs and fixtures to aid in production and welding. The main objective of the jigs and fixtures are to put constraints on the components during the welding process. The jigs must be simple, easy to use, reliable, and capable of reproducing consistent results.
- The jigs served to increase the speed of production, and improve the consistency between products and batches.
- Designing the jigs involved the help and feedback of the production team as they are the ones who will use them.
- I received requests and built specific tools or jigs that the welders thought could improve the production process.
- I spent many hours on the production floor with the production team to understand their actual needs.
- The jigs were mainly made from laser cut sheet metal welded together, and others were 3D printed.
Basin Lid Lifting Tools
During my work, I was tasked with figuring out a standard design for a lift tool and feature to eliminate the need for using direct contact with the drain. The feature and tool must be simple, sanitary, and easy to clean.
- All the basins require skin contact to lift up, which is considered unsanitary, and is ergonomically taxing.
- Involved the sales team in the prototyping process to get feedback on what the customer needs.
- Prototyping went through multiple iterations after getting the feedback until a design was decided on.
- Lids with the lifting tools was first introduced into a specific series, and then later will be introduced to the rest of the slot drains.
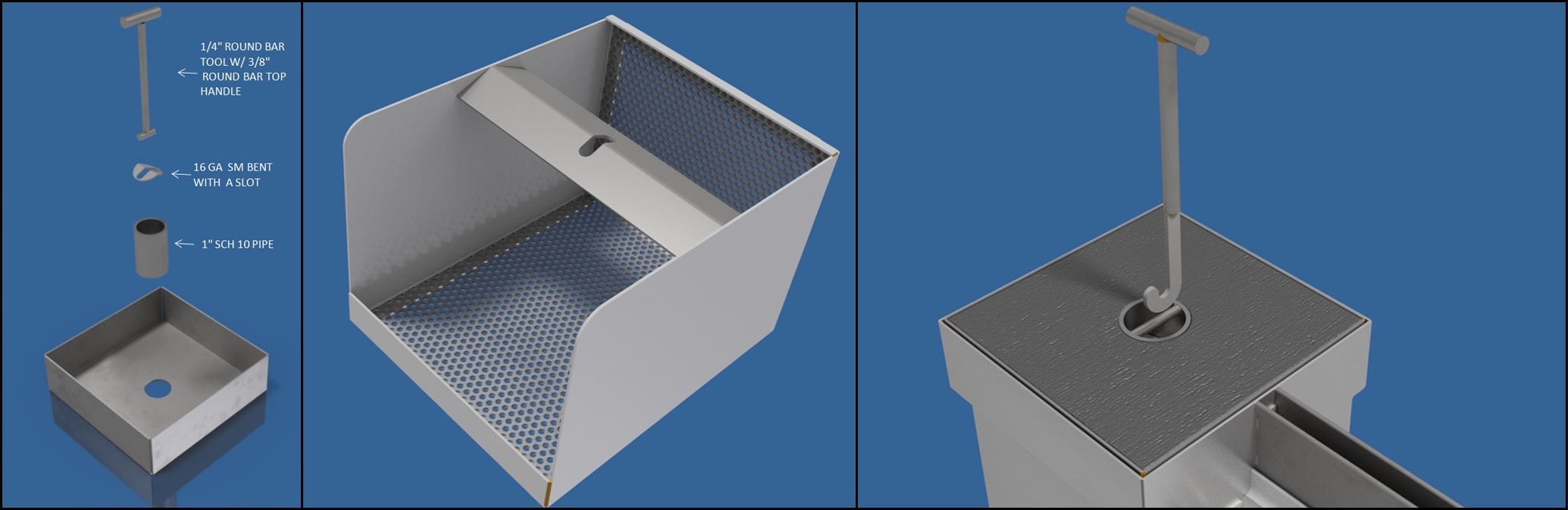
Demo Unit Models
I designed models that helped the sales team demonstrate the features of the drain products. The models were based on the current products but modified to highlight specific aspects of the drains. I also designed and 3D printed smaller models of the slot drain products for the sales team to use as promotions and sales aids.
- Communicated with the sales team during the design process to create the desired units.
- Worked closely with the production team to manufacture the units according to the requirements.
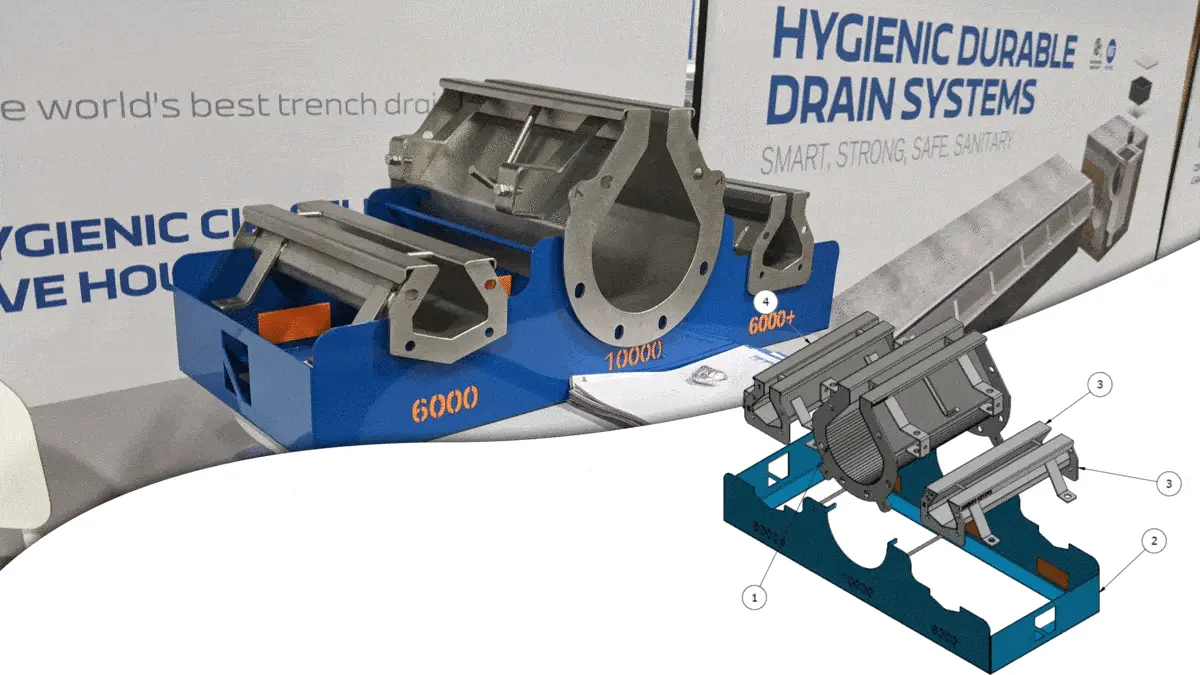
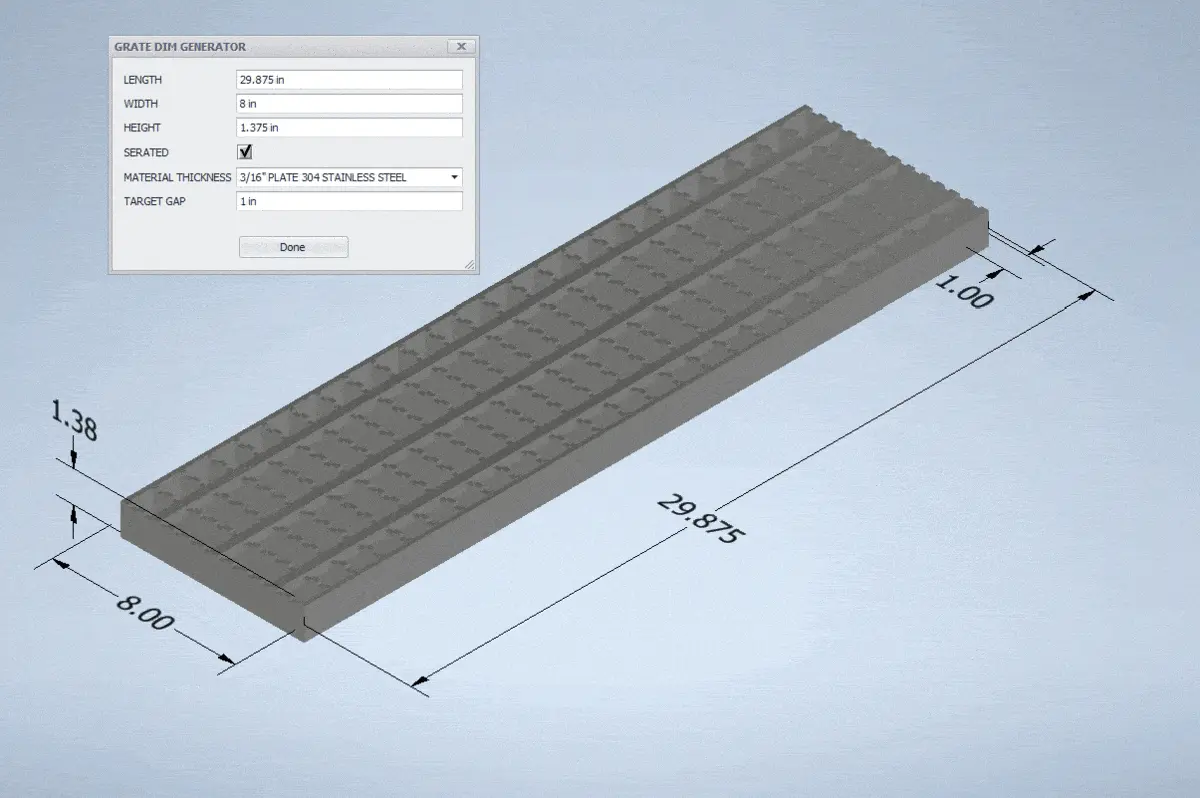