Pipe Expanding Jig
In our work environment, we faced the challenge of centering a drain pipe on the outlet of the drain body. To solve this, we needed a jig that could expand and align the internal circumferences of both the pipe and the drain outlet, facilitating a consistent and easy welding process.
In response to this need, we designed, prototyped, 3D printed, and eventually laser cut the jig. The design underwent several improvements during the prototyping phase.
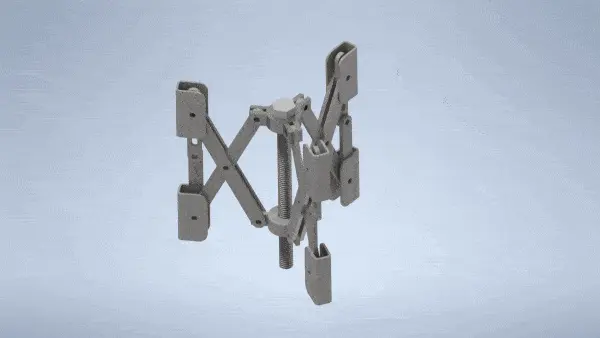
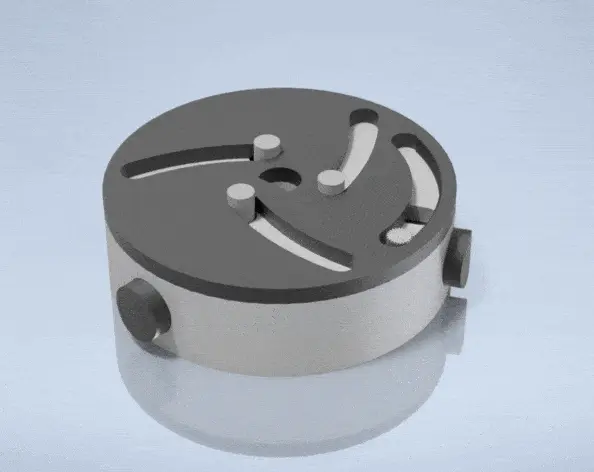
3D Printed Solutions
The following are some challenges and problems that I solved using 3D designed and printed parts:
Hammer Mill Sample Probe Sealer
The Hammer Mill grinds commodities like Corn, Wheat, and Barley. The ground commodities need to be tested to check their micron size level. To take a sample for testing, a probe is inserted into a hole to collect the product. As the hammer mill is under vacuum, the sample probe must seal the hole to correctly grab the sample. However, the probe did not seal, which made sample taking difficult and inaccurate. In response, I designed a sealing piece on Solidworks and 3D printed it. This piece was installed at the neck of the probe to stop the vacuum from leaking.
TV Stand Design
I bought a used TV that was missing its stand. After measuring the dimensions of the TV stand hole on the TV, I designed a replacement using SolidWorks. I then sliced and 3D printed the stand replacement and installed it on the TV.
Phone Dock Design
I designed an ergonomic docking station for my phone to hold it at an angle while charging. The dock holds the charging cable in place, and the cable is detachable from the dock. After building a model of the designed dock in Solidworks, I sliced and 3D printed the dock station.
Cable Holder Design
Under Construction.
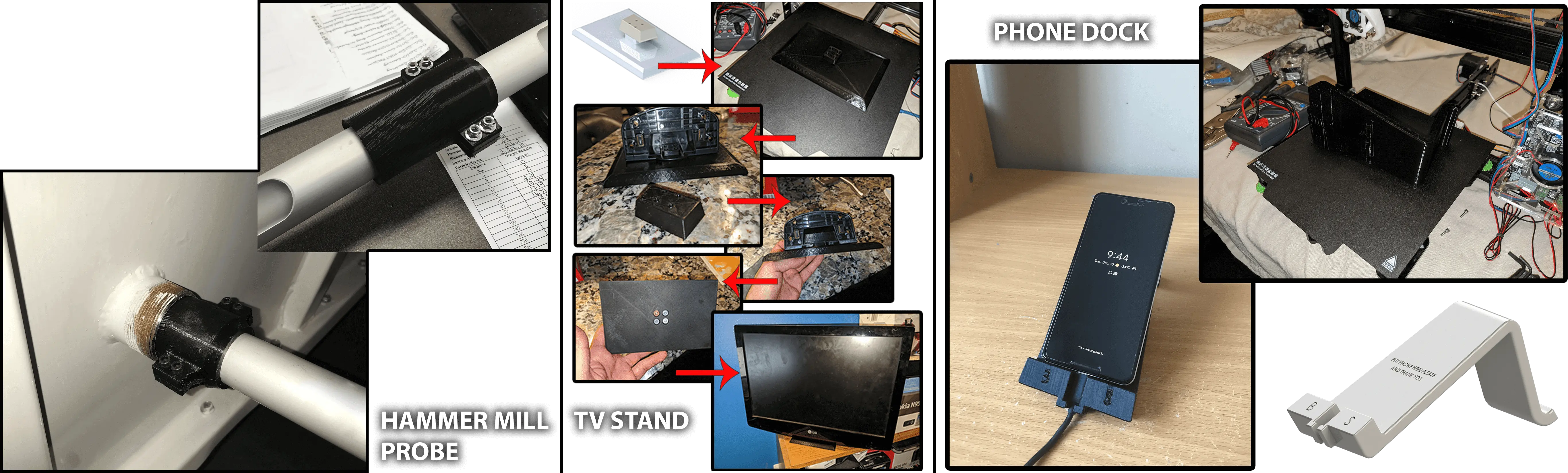
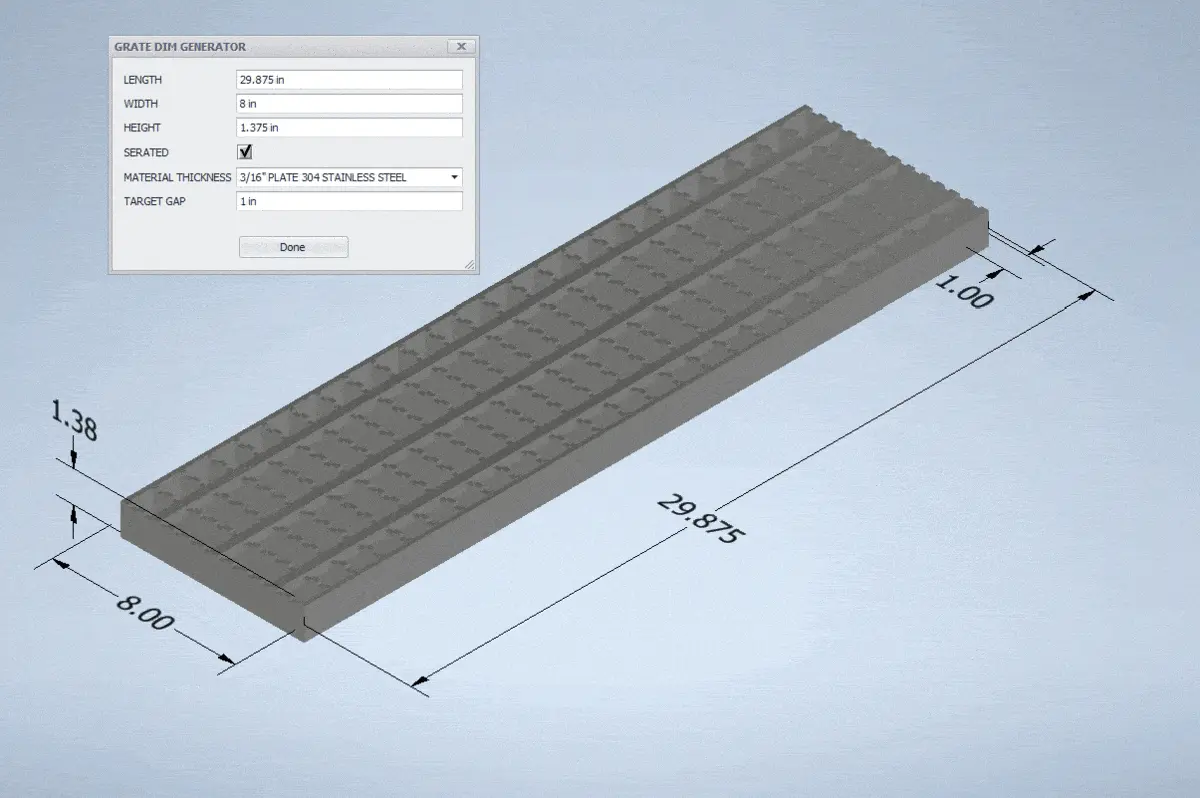
Freezer Requirement For Chinese Products
Our task was to find an efficient solution for reducing our products' internal temperature to -18 degrees Celsius within 48 hours. Upon analysis, it was clear that our main freezer lacked the required capacity to reach these target conditions, and we needed to implement an alternative freezing solution.
We researched various industry solutions, including blast freezers, cryogenic, and contact freezers, listing the advantages and disadvantages of each solution. After thorough consideration, the plate freezers emerged as the best option for our plant needs.
We consulted with thermodynamics literature and used Pham's method to calculate the required time to reach the target temperature. The method showed that we could drop the temperature from 2 degrees Celsius to -18 within just 13.3 hours.
Taking into account the maximum amount of Chinese products produced daily and the sizes of the boxes of these products, we calculated the required dimensions of the plate freezer. Our findings were reported to the continuous improvement manager, who then presented them to the executive committee. The project has now been approved and is in the equipment sourcing phase.