Round Area Drain Design And Production
As a part of my responsibilities at GDT, I was entrusted with the task of researching, designing, and introducing a new product to the company's catalog. This involved conducting extensive research on the customer's needs and the current competitive solutions available in the market. In addition to that, I also reviewed and summarized the National Sanitation Foundation (NSF) specifications to ensure that the designs adhered to their strict guidelines for food safety standards.
I involved all the stakeholders in the process including management, production, engineers, and company owners. With their input, I was able to create a list of customer needs and design different solution prototypes, which were then 3D printed. The area drain product included multiple sub-products that completed the assembly, some standard, others optional. In the process, we faced manufacturing limitations and other challenges, all of which were resolved with adjustments and redesigning.
Ultimately, the manufactured prototypes were used to close a large deal with a major Canadian food producer after implementing solutions to their proposed unique problems. I also implemented a solution to prevent the cover from rotating to avoid slipping. For a detailed account of the project progress, please refer to the attached record: [Link]
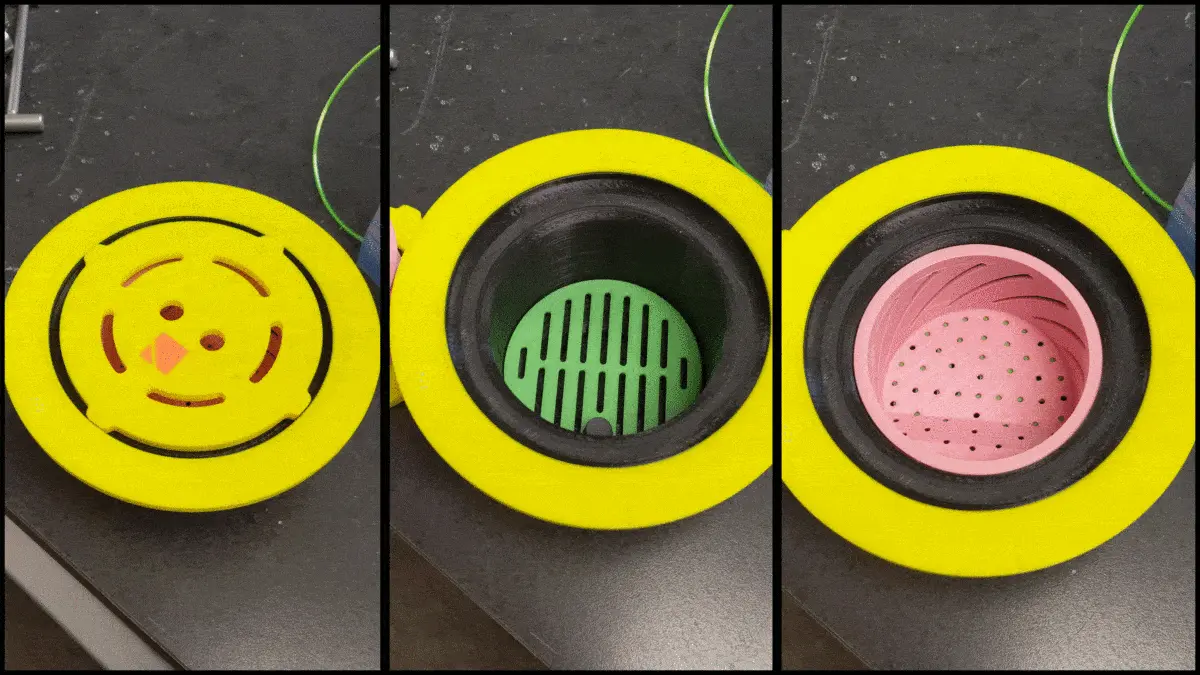
Plastic Drain Improvements
Tasked with the responsibility of improving the production readiness of the plastic slot drain, I undertook several steps to build and assemble the drain runs. This involved creating an assembly line list of materials and equipment required, work in progress, and assembly steps. I also designed multiple jigs to aid each step of the assembly, and a table for the mitre saw that featured a fixturing system and a back fence.
Working closely with the production team, I ensured that the assembly process was conducted efficiently and correctly. This also extended to designing standard and custom basins to meet customer needs, creating stainless steel elbows from one-piece sheet metal to reduce alignment time during welding, and working with a local plastic extrusion company to address assembly challenges. Furthermore, I visited client sites to oversee the drain installation process and gather direct customer feedback.

Cylindrical Cell Material Flow Equipment Technical PM
Under construction.
Commissioning The Thermoformer
As part of the team commissioning the Thermoformer for full-time production, I worked on a multitude of tasks. This included creating a task list and an updated Gantt Chart to keep the project on track, writing test protocols to trial different parameters for the products processed by the Thermoformer, and assisting in organizing and performing tests. The results of these tests were used to calculate the Thermoformer's capacity and required manning.
In addition to these responsibilities, I also assisted in choosing the correct boxes for packaging the Thermoformer-produced packages, creating an SOP for the machine, and deciphering daily error codes. I also worked on modifying the conveyor for a storage area for incoming products and updating the production team on test results.
Commissioning a New Feed Mill
In this project, I was involved in various tasks such as documenting and regularly updating deficiencies in an open issues log, assisting in determining root causes of daily production issues, verifying changes to equipment, and checking and testing equipment capacities. I also tested grind and mash consistency and the micron levels of the ingredients, performed tests to measure the coefficient of variation on the mixer and the pellet durability index, and monitored feed demand across all South West region Feed Mills.
Further tasks included assisting with Open House preparations and presentations to government officials and the public, and designing a choke for the probe used to grab samples from the hammer mills to prevent air vacuum escape during sample extraction.
Overhead conveyors Wear Guards
The new conveyors on the cut floor were causing black foreign material that contaminated the products. In response to this issue, I measured all the lengths and dimensions of the affected conveyors to fabricate wear guards that would stop the belt from rubbing against the metal. I also worked with the sanitation team to identify another source of the foreign material, which was the long rollers spanning the width of the conveyors.
With the help of the maintenance and production team, I created a priority list for which conveyors to tackle first. I maintained contact with the contractor hired to install the wear guards and provided regular updates to the foreign material task force team. In addition, I audited the contractor's work and created an ongoing document to mark progress and deficiencies.
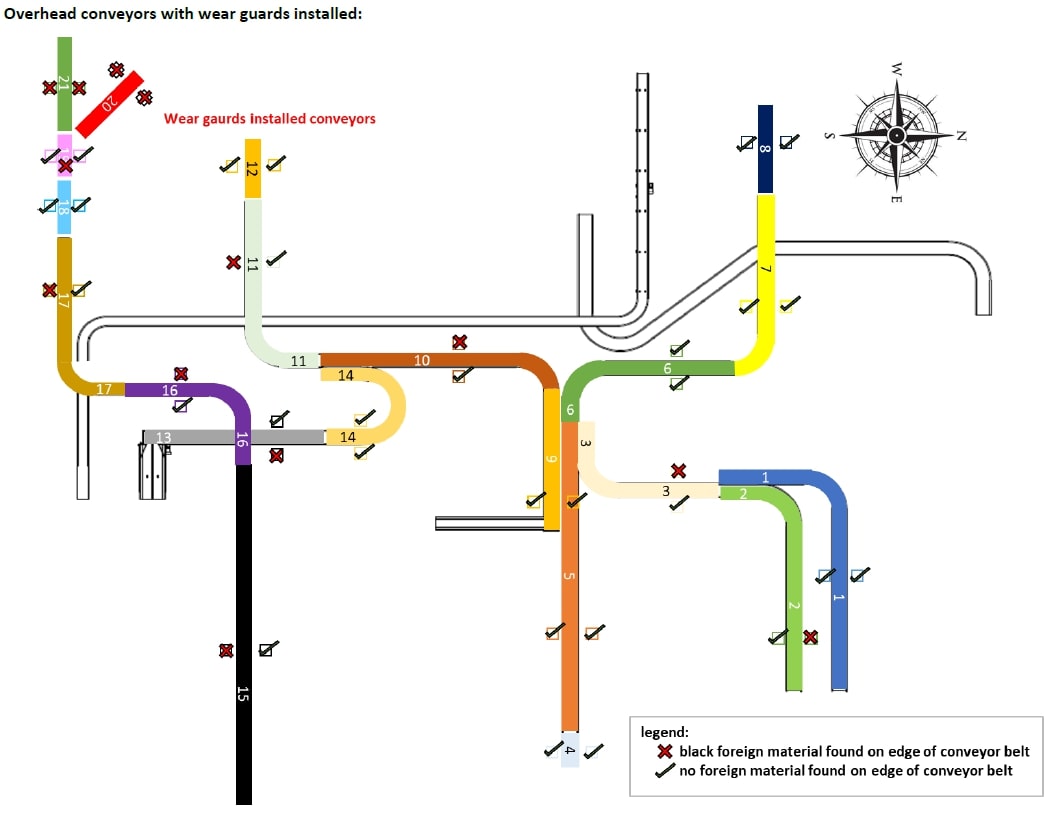
MODA Equipment Commissioning
Under construction.
packaging manufacturing Engineer
Under construction.